Department News
[October Lab Interview] Professor Hoyoung Kim - Microfluidics and Soft Materials Lab
Author
관리자
Date
2024-01-10
Views
407
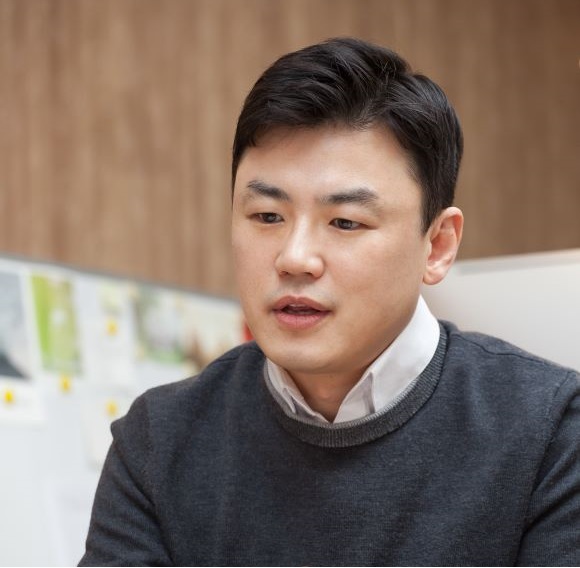
Professor Hoyoung Kim’s Lab: Microfluidics and Soft Materials Lab
Research lab representative Kim Cheong-san
Q1. What is your lab’s research field, and what are its representative studies?
Our lab is researching a wide variety of fields based the mechanics of fluids and soft matter (materials that are difficult to define as solids and liquids). Specifically, (1) fluid behavior and control at the micro/nanoscale, (2) exploration and mathematical understanding of flow phenomena that occur inside and outside living organisms, (3) hydrogels, granular materials, and elastomers. We research basic technologies such as soft mechanical systems using extreme metamorphing of soft materials such as elastomers, as well as applied technologies such as (4) the development of innovative thermal fluid production technologies for secondary batteries and semiconductors.
An interesting example of basic technology is research that interprets natural phenomena. The goal is to discover strange phenomena that go beyond human common sense in the survival and movement patterns of living things, interpret them through mathematical modeling, and explore how this was achieved to find the optimal design point. Representative examples include how efficiently a water strider jumps the water, what are the shapes of fish gills and plant roots optimized for, and how a bird's nest is made so that it can withstand heavy loads even when attached vertically to a cliff. It has been identified.
Meanwhile, industry-related studies include: We are developing a technology for removing impurities or coating the surface of a liquid a high-speed rotating semiconductor wafer, a technology for quickly making secondary battery electrodes with new materials, a microfluidic chip that detects viruses at high speed, and thermal fluid-based mechanical analysis. We are deriving the optimal process and design through .
Q2. Researcher Cheongsan Kim, what kind of research has you conducted and what research are you currently working?
During my master's degree, I studied a pneumatic network (NuNet), a soft robot that deforms when pneumatic pressure is injected into a channel made of polymer. Unlike existing robots, these soft robots have the advantage of notly achieving the desired operability without precise control, but also producing a large force relative to their weight and volume. For example, when grasping an object, existing robots have difficulty precisely controlling the shape of the fingers according to the shape of the object, but soft robots can easily grasp objects of various shapes by adjusting the strength of pneumatic pressure.
In my current doctoral program, I am researching biomechanical machines powered by water using moisture-absorbing and expanding materials (such as wood, sponge, and absorbent gels). Specifically, I am exploring the unique properties of plant-based materials that expand and contract depending the amount of moisture for movement. I interpret this mechanism using principles of mechanical engineering and create new plant-mimicking machines. I primarily use hydrogels, polymers soaked in water, as suitable materials for artificial plant machines, and this technology is expected to be applied in various fields such as wearable devices, flexible displays, artificial organs, and surgical equipment in the future.
Q3. What was the most difficult part of conducting this research and how did you overcome it?
The research I am conducting during my doctoral program involves implementing the principles of plant movement using materials with properties similar to those of plants. This requires a fusion of mechanical and materials engineering. To achieve this, I had to study materials engineering afresh and accumulate my own know-how in material synthesis by referencing various papers. Collaborating with materials engineering and gaining experience in a broader engineering world outside of mechanical engineering has been both challenging and rewarding for me personally.
Q4. Do you have any special devices or equipment in your lab? If not, is there any equipment you often use outside?
We have a variety of equipment to measure various physical properties of materials or manufacture micro/nanoscale machines. We have an Atomic Force Microscope (AFM) that can observe nanoscale surface shapes or measure the elastic modulus of ultrafine objects. We also have Instron's Universal Testing Machine, which can measure the mechanical properties of solids and soft materials, a surface tensiometer for liquids, and a viscometer. We are producing nanofiber mesh and nanoscale 3D printing using electrospinning equipment that creates nanofibers at high speed. In addition, we have various 3D printers, soft material synthesis equipment, high-speed cameras, plasma coating equipment, high-magnification microscopes, spin coaters, etc. Scanning Electron Microscope (SEM) and Environmental Scanning Electron Microscope (ESEM), which are difficult to possess at the individual laboratory level, are used in the school's joint instrument center.
Q5. Any additional comments you would like to share?
One of the challenges I faced as a graduate student was the absence of a definitive answer. There is no model answer for what to research, what manufacturing technology is needed for research, or how to interpret phenomena. In research, you encounter problems for which there is no model answer, and you need to set your own direction and answers. While listening to advice from people around you and evolving based that advice is necessary, fundamentally, you must be able to continuously set your own direction. Moreover, during research, you may find yourself repeating tedious experiments or struggling for days to obtain a single piece of data. When facing such difficulties, I would like to emphasize the importance of cultivating the determination not to give up, as the joy of achievement later is incomparable.
MEch-SSENGER Jeong Seok-cheol