Department News
[JoongAng Daily] Prof. Kyu-Jin Cho: The Future of Soft Robots
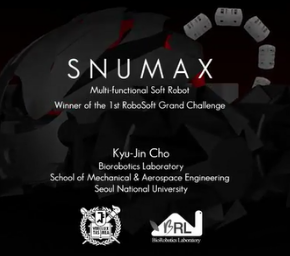
SNUMAX, a robot created by SNU research team, winner of the International RoboSoft Grand Challenge. Its wheels can change shape, and it has arms that bend like the trunk of an elephant. [Video by SNU Soft Robotics Research Center, edited by Hyuk-ju Kwon]
Isaac Asimo, a prominent sci-fi writer, came up with the ‘Three Laws of Robotics’ in 1942. The first law states the following: ‘a robot may not injure a human being.’ Underlying it is the assumption that a robot is, in fact, a danger to humans. But why?
Paradigm Change in Robotics
Flexible and adaptable like a living creatureLimits of metal robots
Made of soft material and able to transform,
‘Soft robots’ are an alternative
Our image of robots come from popular culture, such as Mazinger Z, Transformers, Carbots, Mechanimals, and wearable robot Iron Man. Or we think of robot arms in industrial settings and humanoid robots. All of these examples are robots made of metal or equally hard, durable material. They look dangerous; humans could get easily hurt by just bumping into them. Indeed, in industrial sites, robots operate behind safety nets so that workers don’t get injured.
But are all robots made of such hard material? They cannot be. Robots serve a variety of functions beyond industrial sites. There are autonomous mobile robots, medical robots, search-and-rescue robots, household robots, etc.
Robot with octopus-like movements
There are limits to metallic robots in these types of tasks. They lack flexibility and adaptability. How can metallic search-and-rescue robots approach confined spaces without breaking? Household robots are also required to perform delicate functions, for which metallic robots would be inadequate.
Mini octopus robot created at Harvard. Its power comes from chemical reactions.
That’s why soft robots were born. They are made of rubber or soft plastic. Their movements differ from hard robots as well. Motors do not provide flexibility and elasticity, which is why soft robots employ air pressure, or tension of thin strings in order to move (one such example would be bicycle brakes).
The development of soft robots began in the mid-2000s. In 2007, the Defense Advanced Research Projects Agency (DARPA)of U.S. announced the ‘Chembot program,’ for the purpose of developing robots consisting of flexible material that could perform tasks in confined areas.
Octopus robot created by Prof. Cecilia Laschi and her team of the Sant’Anna School of Advanced Studies, Italy.
In its special edition on soft robotics in 2016, Nature introduced the octopus robot developed by Professor Cecilia Laschi of the Sant’Anna School of Advanced Studies, Italy. The robot is able to grasp objects, bending like an octopus. Prof. Laschi says that she requested her father to catch a live octopus to study its movements while designing the robot.
There have been many advancements in soft robot grippers, which functions like a human hand. Metallic grippers, such as what you would find attached at the end of an industrial robot, are not good at grasping objects with differing sizes and shapes, which is why they had to change the gripper itself to fit the object. Metallic grippers are also insufficient in handling easily breakable objects. The problem can be solved by using a soft gripper.
The research team at SNU developed a tire that changes in size, employing origami principles. The video shows the designing process, the principle behind it, and a demonstration. [Video by SNU Soft Robotics Research Center, edited by Hyuk-ju Kwon]
My research team developed a wheel that changes in size. Imagine an exploration robot in a cave, or a search-and-rescue robot with wheels in a collapsed building, looking for survivors. They would resemble an off-road SUV with large wheels, except smaller in size. Let us suppose the cave grows narrower, or in the case of the collapsed building, the ceiling has broken down—what should the robot do? One solution is to reduce the size of its wheels to make itself smaller.
The team employed origami principles. We actually took origami lessons to make a paper ball that can change its diameter. Based on this, we developed a robot with wheels that change in size and competed in the International RoboSoft Grand Challenge. A Korean tire manufacturer saw this, and contacted us for a size-changing tire to be used in their commercials. So we ended up building a tire for them which could withstand the weight of 1t.
Hankook Tire commercial featuring the size-changing tire
There are plenty of research going on with soft robotics implemented in wearable robots. No one wants to wear an actual Iron Man suit and walk down the street. Wearing heavy machinery on your body is not the most comfortable look. Ideally, wearable robots should look like clothes, while helping the user with any physical disabilities and weaknesses they may have. Like in the movie The Tuxedo starring Jackie Chan.
People often say “Is that even a robot”
Our team has been working on and improving ‘robot gloves’ since 2009. We interviewed a person with disabled arms in order to develop a robot that could assist people in eating food. They said, “I don’t want to be fed. I wish to eat using my own hands.” It came as a surprise. We changed the direction of the research and decided to develop robot gloves made of polymer, which can assist with hand movements instead.
Soft robotic gloves made by SNU research team. They enable people with hand disabilities to pick up objects, turn the doorknob, etc. [Video from SNU Soft Robotics Research Center]
When we first began studying soft robots in late 2000s, a lot of people used to say “are those even robots.” Now, soft robots have entered the mainstream. Now people say “are those even soft robots” to robots that resemble soft robots in movement yet partially consist of metallic material.
I don’t believe in distinguishing soft robots depending on how hard and soft they are. Soft robots are a change in the paradigm of robots. The change came when people questioned dividing robots into joints that move and hard parts that do not move. We should follow the same approach in defining what a soft robot is. Flexible thinking leads to flexible robots and flexible innovations.
Water strider robot that can jump on water like a real water strider. [Video from SNU Soft Robotics Research Center]
◆Prof. Kyu-jin Cho=Developer of SNUMAX, a robot with wheels that can change in size, won the grand prize of the 2016 RoboSoft Grand Challenge held in Italy. After completing his Bachelor’s and Master’s programs at Seoul National University, he received his PhD at MIT. Currently, he is a professor at the Department of Mechanical Engineering and director of the Soft Robotics Research Center at SNU.
Earlier this year, we participated in the Consumer Electronics Show (CES) held in Las Vegas, US. Seoul National University chose what to showcase, but we were somewhat hesitant to go. From what we saw in the media, CES was a platform for cutting-edge technology, ready to be commercialized. But what we had was something that we weren’t sure if it could even be made into a product.
We showcased things like a size-changing wheel, a robot arm that weighs only 28g but can lift 12kg, and a vest-like wearable product that prevents back injury. We had called them ‘dummy solutions’ because we didn’t know how they could be implemented in real life.
The attention we attracted was a shock. Accelerators who work with startups asked us questions, telling us good things. That’s when we realized that new innovative products do not come from a single technology. Rather, they come from a combination of technologies. CES was like a laboratory, where technologies with such potential were demonstrated. No one can guess which technologies can be combined to create something new. CES was a place where technology experts browsed various research and sought potential innovations. We did not need to call our products ‘dummy solutions’ just because we couldn’t think of a way for them to be commercialized.
Our research team has developed a water strider robot. It’s a mini robot that can jump on water like a real water strider. We were able to replicate the jump of a water strider by using a type of metal that shrinks when heat is applied to it. This research was published on Science. We can easily think of the lightweight robot arm we showed at CES being used for a drone, but even I cannot imagine how a water strider robot can be used in real life. However, one thing is for certain: it has plenty of potential to be combined with another technology to create an innovative product.
[Source: JoongAng Daily] [Prof. Kyu-Jin Cho] The Future of Soft Robots
Link to article https://news.joins.com/article/23736110